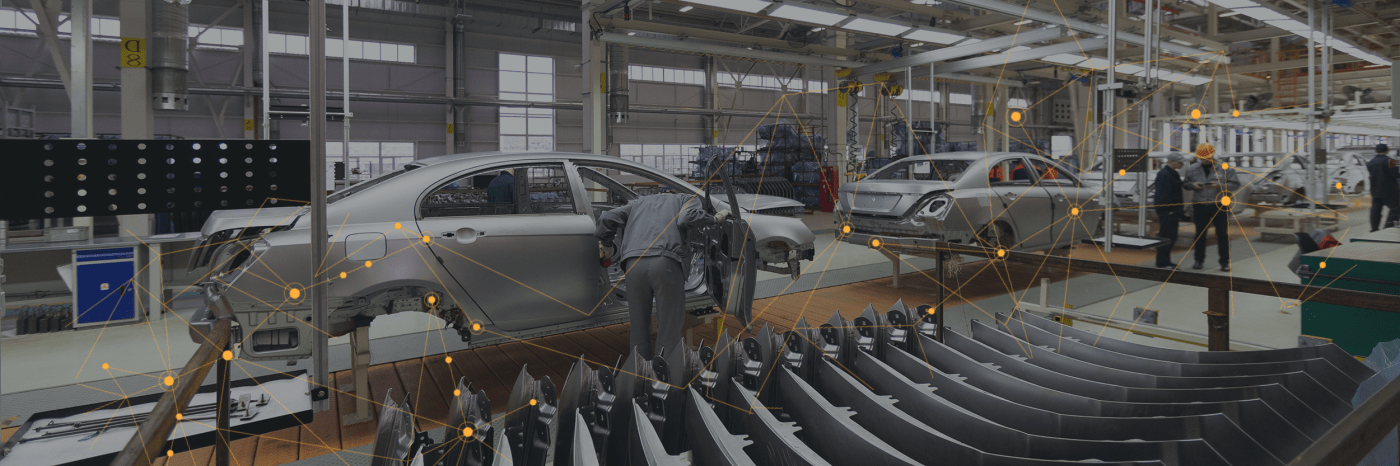
- Manufacturing
- Case Study
Achieve Production Planning Excellence
Key Facts
+10%
operational efficiency
50 min.
to first results
3,500
decision variables
operational efficiency
to first results
decision variables
Our client is an international car manufacturer that has to adapt to a very competitive market and uncertain environment. He needed to boost the production of specific engines to meet an increasing demand with the same capacity.
The company’s main challenge was to ensure that the production of assembled engines met customer demand, every week, over a fifty-two week period. They needed a software solution that could anticipate the effect of bottlenecks on the whole organization and take into account the following factors:
With Cosmo Tech Supply Chain, a realistic and exhaustive Prescriptive Simulation Twin of the whole engine production system was deployed. The software was designed to:
Thanks to the Cosmo Tech Production Planning Software, tens of thousands of simulations were executed to create, in less than 20 minutes, the optimal production plan with the current supply chain configuration.
Using our simulation software solution, the production planning manager was able to identify crucial bottlenecks on two heat treatment machines. He easily experimented with various realistic what-if scenarios and in this specific case, found that the optimal solution to meet demand was to negotiate with one specific contractor and increase the amount of products coming from his factory.
Thanks to Cosmo Tech, our supply chain network is modeled. As soon as a variable changes, we can easily recalculate the optimum.
With Cosmo Tech Supply Chain, our client was able to significantly increase the number of manufactured engines and created value in less than a quarter.
By using our Pre-packaged Simulation Twin Solution, our client was able to:
Contrary to traditional approaches which cannot test this level of detail and do not consider time or uncertainty, Cosmo Tech Supply Chain provided a dynamic simulation-based optimization method to solve our client’s complex supply chain problems.